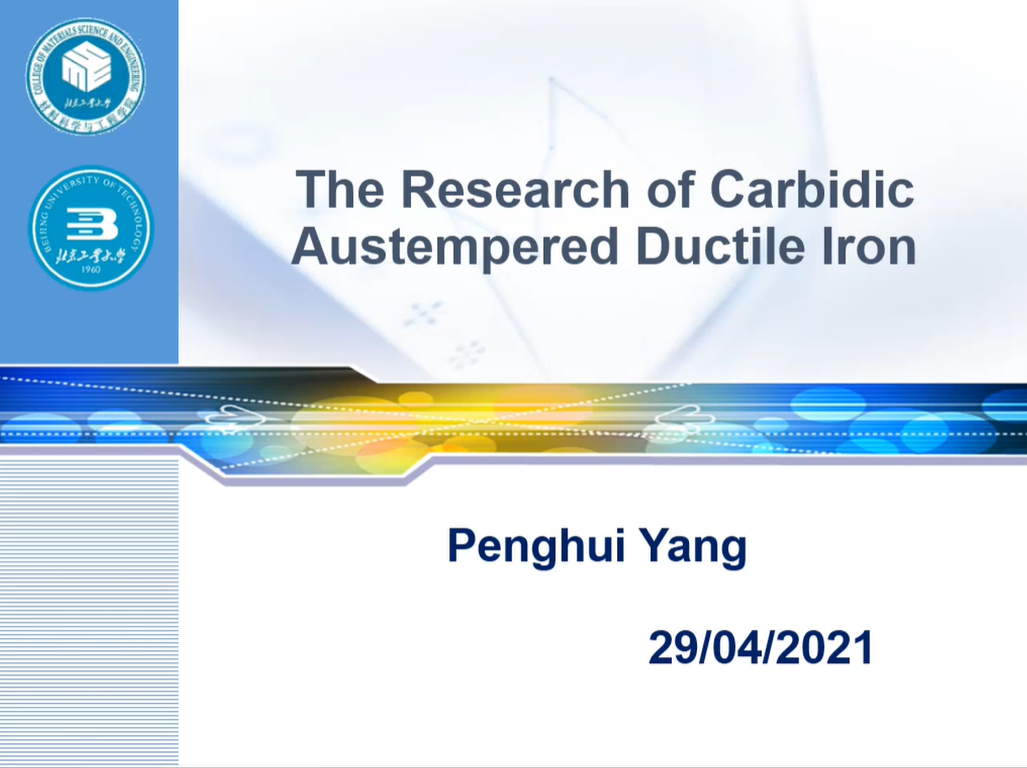
Research of Carbidic Austempered Ductile Iron
Penghui YANG
Automatique Non-linéaire et énergies renouvelables
Chers collègues,
J’ai le plaisir de vous annoncer le séminaire de
Penghui YANG, portant sur " Research of Carbidic Austempered Ductile Iron ", thème Automatique Non-linéaire et énergies renouvelables
le 29/04 à 13h via Teams.
Résumé :
Grinding balls in wet ball mill are an important consumables in mine grinding equipment, which have poor wear resistance and large consumption. It is imperative to find excellent wear-resistant materials for the grinding balls. Carbidic Austempered Ductile Iron (referred to as CADI) was used as small and medium-sized wet ball mills. This grinding ball has the advantages of less wear, low crushing rate, power saving and low noise. However, the CADI grain boundaries are distributed with net-like eutectic carbides, which seriously damages the continuity of the matrix. In addition, the mechanism of corrosion wear and impact fatigue is lack of research due to complex phase composition and unclear mechanism of phase properties on improving performance. So CADI can’t be applied to the grinding balls in large wet ball mill. The heterogeneous nucleation mechanism and adsorption mechanism of microalloying elements on M3C carbides were analyzed by the first principles from the atomic scale, which predicted the possibilities of microalloying to regulate the size, morphology and distribution of eutectic carbides in CADI. Then the effect of the microalloying on CADI was verified through experiments. The simulation results showed that after adding the modification elements Nb and Ti, NbC and TiC particles could be precipitated previously act as the effective heterogeneous nucleation of M3C, destroyed the carbide network. The experimental results show that the net-like structure of carbides was destroyed by microalloying, which improved the impact toughness and the wear resistance of CADI.
Finally, the failure mechanism of impact fatigue and corrosive wear was revealed by characterizing the sample surface and the cross-section after corrosive wear and impact fatigue. Corrosive wear failure mechanism : The matrix is first corroded, which led to breakage and exfoliation of carbides, causing CADI corrosive wear failure. Impact fatigue failure mechanism : a large number of impact fatigue cracks were produced due to the deformation of graphite nodules and the fracture of carbides, resulting in the intergranular fracture. In addition, the grains had no obvious preferred orientation after impact fatigue, but the grains had a tendency of the grain refinement and the increase of low-angle grain boundaries. The potential difference between graphite nodule and matrix was reduced by adding Cu element, which improved the corrosion resistance and corrosive wear resistance of CADI.
En vous souhaitant un très bon séminaire,
Cordialement,
Equipe de valorisation scientifique de QUARTZ.